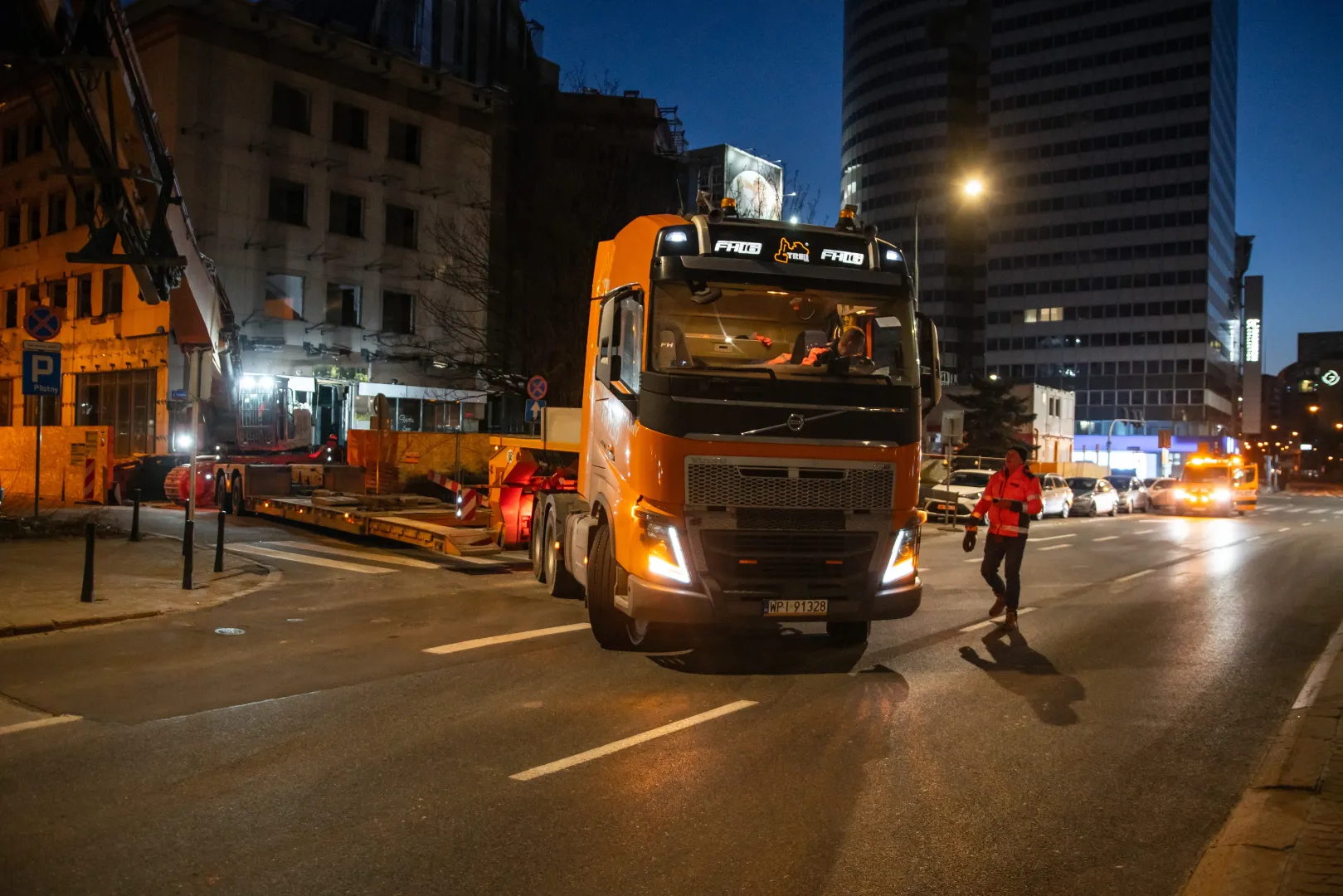
Efficiency Analysis of Liebherr Machines in High-Rise Building Demolition Processes
Comprehensive efficiency analysis of Liebherr demolition excavators in high-rise building demolition projects. The study covers operational parameters, fuel consumption, and the impact of operator tec
Efficiency Analysis of Liebherr Machines in High-Rise Building Demolition Processes
Abstract
This technical analysis presents the results of a comprehensive study on the efficiency of Liebherr demolition machines in the context of high-rise building demolition. The study was conducted based on data collected from 12 demolition projects carried out by the TREE Group between 2021 and 2023. The analysis focuses on operational parameters, fuel consumption, work efficiency, and the impact of operator techniques on the effectiveness of the entire demolition process.
1. Introduction
Demolition of high-rise buildings is one of the most demanding tasks in the demolition industry. It requires the use of specialized equipment that must meet rigorous safety, efficiency, and precision requirements. Liebherr machines, particularly the R 950 Demolition and R 960 Demolition models, are widely used in such projects.
The aim of the analysis was to determine the actual efficiency of these machines under operational conditions and to identify factors affecting their effectiveness. The results have practical applications in planning demolition projects, cost optimization, and operator training.
2. Research Methodology
2.1 Scope of Research
The analysis includes data collected from 12 demolition projects carried out by the TREE Group, in which a total of 8 Liebherr machines were used (4 R 950 Demolition models and 4 R 960 Demolition models). The projects were implemented in various urban conditions and with different types of building structures.
2.2 Data Collection
Data was collected using:
- Telemetry systems installed in machines
- Operator work logs
- Time measurements of individual demolition stages
- Cameras monitoring machine operation
- Fuel consumption measurements
2.3 Analyzed Parameters
The study considered the following parameters:
- Operational efficiency (m³ of demolished structure/hour)
- Fuel consumption (l/h and l/m³ of demolished structure)
- Work cycle times
- Impact of operator experience on efficiency
- Failures and technical downtime
- Impact of demolition techniques on overall efficiency
3. Analysis Results
3.1 Operational Efficiency
The average operational efficiency for the analyzed machines was 18.4 m³/h for the R 950 Demolition model and 23.6 m³/h for the R 960 Demolition model. Significant differences in efficiency were observed depending on:
- Building structure type (reinforced concrete, steel, mixed)
- Working height
- Operator experience
- Weather conditions
Machine Model | Average Efficiency (m³/h) | Min. Efficiency (m³/h) | Max. Efficiency (m³/h) |
---|---|---|---|
R 950 Demolition | 18.4 | 12.2 | 25.7 |
R 960 Demolition | 23.6 | 15.8 | 31.2 |
3.2 Fuel Consumption
Fuel consumption showed a strong correlation with work intensity and the type of structure being demolished. The average fuel consumption is as follows:
Machine Model | Average Consumption (l/h) | Consumption per Unit Volume (l/m³) |
---|---|---|
R 950 Demolition | 38.2 | 2.08 |
R 960 Demolition | 45.7 | 1.94 |
The analysis showed that despite higher absolute fuel consumption, the R 960 Demolition model achieves better fuel efficiency per unit volume of demolished structure.
3.3 Impact of Operator Experience
The study showed a significant impact of operator experience on machine efficiency. Operators with more than 5 years of experience achieved on average 27% higher efficiency compared to operators with less than 2 years of experience. The most important factors affecting efficiency differences are:
- Ability to select the optimal demolition technique
- Precision in controlling the demolition arm
- Effectiveness in managing machine power
- Ability to predict structural behavior during demolition
3.4 Failures and Technical Downtime
The average failure-free operation time for the tested machines was 285 hours for the R 950 Demolition model and 312 hours for the R 960 Demolition model. The most common causes of technical downtime were:
- Hydraulic system damage (42% of cases)
- Problems with demolition attachments (31% of cases)
- Electronic failures (18% of cases)
- Other (9% of cases)
4. Optimization of Demolition Techniques
Based on the conducted research, optimal demolition techniques for different types of structures were identified:
4.1 Reinforced Concrete Structures
For reinforced concrete structures, the most effective technique proved to be gradual demolition from the top using a hydraulic hammer in the first phase (to crush concrete) and hydraulic shears in the second phase (to cut reinforcement). This combination allowed achieving efficiency 18% higher compared to demolition using only a hydraulic hammer.
4.2 Steel Structures
For steel structures, the highest efficiency was achieved using steel cutting shears, with precise planning of cutting sequences to control the collapse of structural fragments. This technique reduced fuel consumption by about 15% compared to other methods.
4.3 Mixed Structures
For mixed structures, a protocol for sequential attachment changes was developed, minimizing the time needed to change tools. Precise planning of the demolition sequence of individual structural elements also proved to be a key factor.
5. Economic Analysis
The economic analysis showed that optimally selected machines and demolition techniques can bring savings of 15-22% of the total cost of a demolition project. Based on data from the analyzed projects, the average cost of demolishing 1 m³ of structure was:
- Using optimal techniques: 78.3 PLN/m³
- Using standard techniques: 95.8 PLN/m³
6. Conclusions and Recommendations
6.1 Conclusions
Based on the conducted analysis, the following conclusions were formulated:
Liebherr machines from the Demolition series show high efficiency in high-rise building demolition processes, especially the R 960 Demolition model.
Operator experience is a key factor affecting work efficiency, with efficiency differences reaching up to 27%.
Appropriately selected demolition techniques can bring savings of 15-22% of the total project cost.
Regular operator training and systematic machine maintenance can significantly increase efficiency and reduce the risk of failures.
6.2 Recommendations
Based on the conducted analysis, the following is recommended:
Introduction of systematic training for operators, focused on optimal demolition techniques.
Implementation of real-time machine efficiency monitoring systems.
Development of detailed demolition plans taking into account the specifics of the structure and selection of optimal attachments.
Implementation of a preventive machine maintenance program, particularly targeting hydraulic systems, which are the most common cause of failures.
Consideration of investing in newer machine models for projects requiring particularly high efficiency.
7. Bibliography
- TREE Group internal data from demolition projects 2021-2023
- Technical specifications of Liebherr R 950 Demolition and R 960 Demolition machines
- Krause, J. (2021). "Efficiency in High-Rise Demolition Projects". Journal of Construction Engineering, vol. 45, pp. 128-142
- Liebherr Group (2022). "Technical Handbook for Demolition Excavators"
- Nowicki, M., Kowalski, T. (2022). "Comparative Analysis of Demolition Techniques in Urban Conditions". Engineering and Construction, no. 3, pp. 78-92
The analysis was prepared by the Research and Development Department of the TREE Group based on data from actual demolition projects. The results have practical applications in planning and implementing demolition projects and in the process of training machine operators.
Tags
Share this analysis
About the author
dr inż. Marek Nowicki
Head of Research and Development at TREE Group
Category
Analizy procesów wyburzeniowych
Reading time
15 minutes
Publication date
March 18, 2025
Available in other languages
🇵🇱 Polish versionSimilar analyses
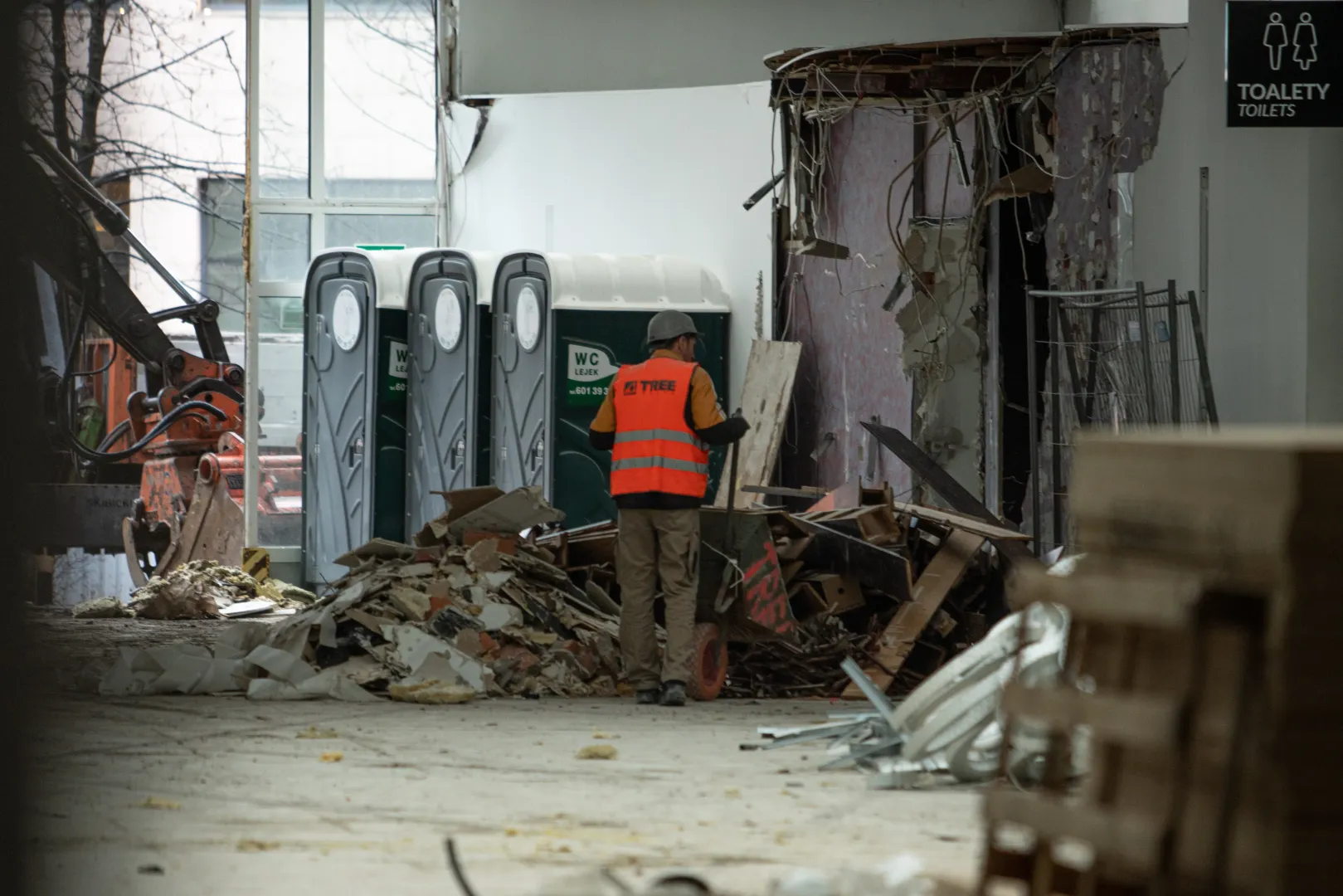
Modern Demolition Technologies: Comparative Analysis and Development Trends
Comprehensive analysis of contemporary demolition technologies, their efficiency, environmental impact, and economic via...