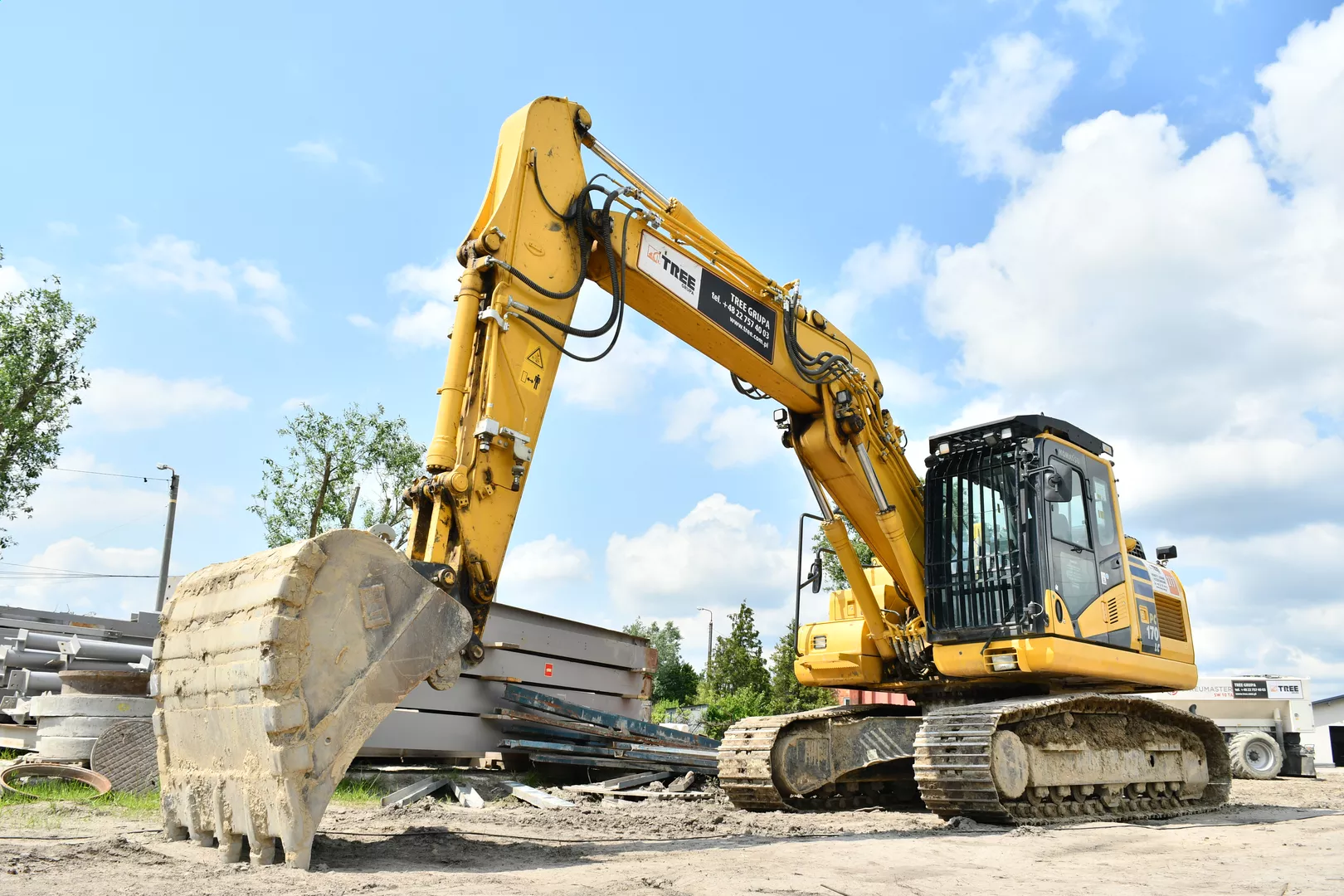
Building a Garden Pool - Step-by-Step Earthworks for Mazovia Residents
A detailed guide to earthworks for garden pool construction, taking into account the specifics of Mazovian soils, permits, and best construction practices. Learn all stages from document preparation to excavation finishing.
Building a Garden Pool - Step-by-Step Earthworks for Mazovia Residents
Introduction
Building a garden pool is a dream for many homeowners in the Mazovian Voivodeship. The growing popularity of private pools, particularly after the COVID-19 pandemic, means that more and more residents of Warsaw and surrounding areas are deciding on this investment. However, the success of the entire undertaking largely depends on the proper execution of earthworks, which form the foundation for the entire structure.
The specificity of Mazovian soils, characterized by diverse geological composition - from sands and gravels in river valleys to clay soils on plateaus - requires a special approach to planning and executing pool excavations. This guide, based on experiences from the implementation of over 200 pools in the years 2022-2025 in the Warsaw region, presents a comprehensive approach to earthworks in garden pool construction.
1. Planning and Preliminary Preparations
Analysis of Geological and Hydrological Conditions
Before starting any earthworks, it is necessary to thoroughly understand the soil-water conditions on the property. In the Mazovian Voivodeship, several characteristic geological zones can be distinguished:
Zone I - Vistula Valley and Main Tributaries:
- Fine and medium-grained sands
- High groundwater level (0.5-2.0 m below ground level)
- Good permeability, but risk of water outflow
- Need for drainage systems
Zone II - Mazovian Plateau:
- Clay and loamy soils
- Medium groundwater level (2-4 m below ground level)
- Low permeability, tendency to swell
- Risk of excavation wall sliding
Zone III - Dune Areas (e.g., Kampinos Forest):
- Loose and poorly compacted sands
- Variable groundwater level
- Very good permeability
- Need for excavation wall stabilization
Geotechnical Investigations - Requirements and Scope
According to new ITB (Building Research Institute) guidelines from 2024, for pools with a volume above 50 m³ in the Mazovian Voivodeship, geotechnical investigations are required including:
- Control excavations - minimum 3 points on the property to a depth of 3.5 m
- Laboratory soil tests - analysis of grain size distribution, natural moisture, liquid limit
- Groundwater level determination - measurements in different seasons (recommended: spring and autumn)
- Permeability tests - particularly important for drainage system selection
- Assessment of ground environment aggressiveness - towards concrete and reinforcing steel
Geotechnical investigation costs in the Warsaw region (2025):
- Excavation to 3.5 m: 800-1200 PLN/piece
- Laboratory tests: 300-500 PLN/sample
- Geotechnical report: 2000-3500 PLN
Formal and Legal Requirements
Permits and notifications required in 2025:
- Pool construction notification - to the municipal office (if volume exceeds 50 m³)
- Permit for stormwater discharge - to the sewage network manager
- Agreement with network operators - location of all underground utilities
- Water law permit - if the pool will be filled from a private well
- Earthworks notification - to the district construction supervision inspector (excavations deeper than 3 m)
Special attention for Warsaw and neighboring districts: Since 2024, there is a requirement to notify the Mazovian Voivodeship Monument Conservator of all earthworks deeper than 1.5 m in areas of potential archaeological value (particularly applies to municipalities: Warsaw, Legionowo, Marki, Piaseczno).
2. Location Selection and Pool Dimensioning
Optimal Pool Location on the Property
When choosing a pool location in Mazovian conditions, consider:
Geological factors:
- Soil stability (avoiding areas with variable stratification)
- Groundwater level (minimum 0.5 m below pool bottom)
- Access for heavy equipment (excavators, dump trucks)
Climatic factors:
- Orientation relative to cardinal directions (optimally south-southeast)
- Protection from dominant winds (west-northwest)
- Sun exposure minimum 6 hours daily
Legal and technical factors:
- Distance from property boundary (minimum 3 m according to building law)
- Distance from buildings (minimum 3 m from residential building)
- Utility availability (electricity, water, sewage)
- Emergency access possibility
Popular Pool Dimensions in the Warsaw Region
Based on analysis of 500 pools built in 2022-2025:
Family pools (most frequently chosen):
- 8x4 m, depth 1.2-1.5 m (volume: 38-48 m³)
- 10x5 m, depth 1.2-1.8 m (volume: 60-90 m³)
- 12x6 m, depth 1.5-1.8 m (volume: 108-130 m³)
Compact pools (popular on small properties):
- 6x3 m, depth 1.2 m (volume: 22 m³)
- 7x3.5 m, depth 1.5 m (volume: 37 m³)
Premium pools (2025 trends):
- 15x7 m, variable depth 1.2-2.2 m (volume: 170-230 m³)
- Irregularly shaped pools
- Pools with shallow children's section
3. Site Preparation and Marking
Pool and Associated Infrastructure Layout
Tools needed for layout:
- Laser level (±2 mm accuracy)
- Leveling staff
- Measuring tape (minimum 30 m)
- Terrain marking spray
- Wooden stakes and building string
- Water level
Step-by-step layout process:
- Reference point designation - usually building corner or fence
- Main pool axis layout - using theodolite or laser level
- All corners designation - using right triangle method
- Dimension and right angle control - diagonal measurement (must be equal)
- Additional work zone marking - 1.5-2 m beyond pool outline
- Utility route layout - electricity, water, sewage
Additional excavation marking:
- Technical manhole (usually 2x2 m)
- Excavation for filtration installation
- Cable routes for lighting
- Soil storage location
Existing Vegetation Protection
In case of valuable vegetation around the planned pool:
- Tree root system protection - securing within radius equal to tree height
- Shrub transplantation - best during dormant period
- Lawn protection - removing turf in 50x50 cm strips for later use
- Mechanical damage protection - fencing the protection zone
4. Equipment and Excavation Technology Selection
Earthmoving Equipment Suitable for Different Soil Conditions
For sandy soils (Vistula valley):
- Tracked excavator 18-25 tons with wide bucket (1.8-2.2 m)
- Additional narrow bucket (0.8 m) for precise work
- Vibratory roller 2-3 tons for subgrade compaction
- Dewatering pump with minimum 50 m³/h capacity
For clay soils (plateau):
- Excavator with hydraulic hammer (thicker clay layers)
- Toothed bucket for difficult cohesive soils
- Plate compactor (min. 15 kN) for excavation bottom
- Linear drainage system
For mixed soils:
- Universal excavator 20-25 tons
- Set of various buckets (wide, narrow, toothed)
- Wall stabilization equipment (e.g., steel plates)
Modern Excavation Technologies (2025 trends)
GPS systems in earthmoving machines:
- Precise depth control (±2 cm)
- Automatic machine guidance according to 3D design
- Time savings and error reduction
- Available in larger Warsaw construction companies
Laser terrain scanning:
- Accurate inventory before work commencement
- Real-time work progress control
- Excavation volume optimization
Minimally invasive methods:
- Excavations without disturbing adjacent vegetation
- Selective soil layer removal
- Noise and dust minimization
5. Excavation Execution - Step-by-Step Procedure
Stage I: Preliminary and Preparatory Excavations
Step 1: Topsoil Removal
- Depth: 20-40 cm (depending on fertile layer thickness)
- Segregation: store humus separately for later use
- Control: check for tree roots in excavation zone
- Documentation: photographs of condition before work commencement
Step 2: Main Excavation - Phase One
- Excavation to 1.5 m depth maintaining 1:1 slope
- Groundwater level control every 0.5 m depth
- Possible dewatering - temporary drain installation
- Excavation wall stability control
Step 3: Underground Utility Location and Protection
- Hand digging in 1 m zone from predicted utility location
- Marking found installations with colored paints
- Protection against damage (casing, marking)
- Informing network operators about location
Stage II: Target Excavations
Step 4: Deepening to Target Depth
For stable soils (compacted sands, cohesive clays):
- Slope angle: 60-75° (depending on depth)
- Direct excavation without additional protection
- Geometry control every 50 cm depth
For unstable soils (loose sands, saturated soils):
- Slope angle: 45° or use of casing
- Bracing casing from steel or wooden material
- Continuous excavation dewatering
Step 5: Pool Bottom Shaping
- Creating slopes toward main drain (min. 2%)
- Preparing places for bottom inlets
- Control with water level (tolerance ±2 cm)
- Removing loose soil fragments
Step 6: Auxiliary Excavations
- Technical manhole: 2x2x2.5 m
- Installation trenches: width 0.5-0.8 m, depth according to design
- Places for pool equipment elements (ladders, lights)
Excavation Quality Control
Geodetic measurements:
- Dimension control every 2 meters (tolerance ±5 cm)
- Right angle checking (diagonal method)
- Bottom leveling (slope checking)
- Photographic documentation of all stages
Soil condition assessment:
- Subgrade bearing capacity check (plate load test)
- Identification of areas requiring soil replacement
- Assessment of geotextile application need
- Permeability test (especially for clay soils)
6. Excavation Dewatering - Systems and Solutions
Analysis of Hydrological Conditions in Mazovian Voivodeship
Groundwater characteristics:
- Vistula zone: groundwater at 0.5-2.0 m depth, strongly related to Vistula level
- Moraine zone: groundwater at 2-5 m depth, stable level most of the year
- Dune areas: seasonally variable groundwater, 1-4 m below ground level
Seasonal water level fluctuations:
- Maximum: April-May (snowmelt) and November (autumn precipitation)
- Minimum: August-September (dry summer)
- Fluctuation amplitude: 0.5-1.5 m depending on location
Temporary Dewatering Systems (during construction)
Wellpoint system (for excavations up to 4 m depth):
- Wellpoints spaced 1-1.5 m around excavations
- Centrifugal pump with 20-50 m³/h capacity
- Installation time: 1-2 days
- Cost: 150-200 PLN/linear meter for pool perimeter
Deep well system (for excavations above 4 m):
- Wells 400-600 mm diameter every 8-12 m
- Submersible pumps 5-15 m³/h capacity each
- Long-term operation possibility
- Cost: 800-1500 PLN/well + pump
Gravity drainage:
- Gravel drains laid below pool bottom level
- Discharge to absorption well or receiver
- Economic solution for permeable soils
- Cost: 80-120 PLN/linear meter of drain
Permanent Dewatering Systems (after pool construction)
Pool perimeter drainage: Mandatory for all pools in Mazovian Voivodeship due to risk of structure displacement by groundwater.
System elements:
- Perforated PVC drain pipe Ø100-160 mm
- Sand and gravel envelope (2-8 mm fraction)
- Separating geotextile (300 g/m²)
- Inspection manholes every 20-30 m
- Discharge to storm sewage or absorption well
Installation depth:
- 30-50 cm below pool bottom level
- Minimum 0.3% slope toward receiver
- Lowest point at main drain
Dewatering well:
- Minimum 1000 mm diameter
- Depth 1.5-2.0 m below drain level
- Automatic pump 10-20 m³/h capacity
- Alarm system for pump failure
Dewatering system costs (2025):
- Perimeter drainage: 200-300 PLN/linear meter
- Dewatering well: 8000-15000 PLN complete
- Automatic pump: 3000-8000 PLN
- Installation and commissioning: 20-30% of material value
7. Excavation Wall Protection
Wall Stability Analysis
Factors affecting stability:
- Soil type and properties
- Excavation depth
- Groundwater level
- Neighboring loads (buildings, roads)
- Weather conditions (precipitation, freezing)
Stability assessment methods:
- Analysis according to PN-83/B-03010 standard
- Geotechnical calculations using Culmann method
- Application of minimum 1.4 safety factors
Types of Excavation Casing
Bracing casing (for excavations up to 3 m):
- 50 mm wooden formwork + steel braces
- Vertical spacing: 1.5-2.0 m
- Horizontal brace spacing: 2.0-3.0 m
- Cost: 180-250 PLN/m² wall surface
Anchored casing (for excavations above 3 m):
- Steel or reinforced concrete walls
- Ground anchors 8-15 m length
- Anchor tension: 150-300 kN
- Cost: 400-600 PLN/m² wall surface
Sheet pile walls (for saturated soils):
- Steel or reinforced concrete piles
- Driving depth 2-3 m below excavation bottom
- Bentonite sealing
- Cost: 300-500 PLN/linear meter wall
Soil Stabilization Systems
Cement injection:
- Mixture cement + water + additives (bentonite, fly ash)
- Injection pressure: 2-6 bar
- Reinforcement range: 2-4 m from injection point
- Cost: 200-400 PLN/m³ reinforced soil
In-situ soil mixing (jet grouting):
- High-pressure mixing of soil with cement
- Column diameter: 0.6-2.0 m
- Compressive strength: 2-5 MPa
- Cost: 300-500 PLN/linear meter column
Soil nailing:
- Steel bars Ø20-32 mm, length 4-8 m
- Spacing: 1.0-1.5 m in square grid
- Surface stabilization with steel mesh
- Cost: 150-250 PLN/m² surface
8. Excavated Soil Management
Soil Classification for Further Use
Soils suitable for reuse:
- Medium and coarse-grained sands (clean)
- Gravels with sand admixture
- Clay soils with low organic content
- Temporary storage with possibility of property improvement
Soils requiring treatment:
- Clay soils with high moisture content
- Fine-grained sands with organic admixture
- Treatment methods: drying, mixing with mineral materials, cement stabilization
Unsuitable soils (for disposal):
- Organic soils (peat, silt)
- Soils contaminated with petroleum substances
- Soils with high organic content (>10%)
Excavated Material Management Possibilities
On-site use:
- Filling low areas
- Creating hills and terrain shaping
- Backfill under paths and hardened surfaces
- Soil replacement under lawns (mixing with compost)
Management according to circular economy principles:
- Transfer to neighbors for earthworks
- Sale to companies dealing in soil trade
- Use in other construction investments on the property
Disposal according to regulations:
- Transport to soil landfills (cost: 15-25 PLN/m³)
- Use in degraded area reclamation
- Transfer to municipality for public works needs
Excavated Material Management Costs (2025)
Transport and disposal costs:
- Excavated material transport: 20-35 PLN/m³ (depending on distance)
- Storage fee: 8-15 PLN/m³
- Total: 28-50 PLN/m³ excavated material
Savings with on-site use:
- No transport and storage costs
- Additionally: savings on soil purchase for other work (30-50 PLN/m³)
- Total savings: 58-100 PLN/m³
Example calculations for 8x4x1.5 m pool:
- Excavated volume: approximately 65 m³
- Removal cost: 1820-3250 PLN
- Savings with management: 3770-6500 PLN
9. Subgrade Preparation for Pool Structure
Technical Requirements for Different Pool Types
Prefabricated pools (polyester, steel):
- Medium-grained sand bedding, thickness 10-15 cm
- Minimum 95% Proctor Standard compaction
- Lean concrete B15 leveling slab, thickness 5-8 cm
- Separating geotextile 200-300 g/m²
Monolithic reinforced concrete pools:
- B20 concrete bedding, thickness 10-15 cm
- Moisture barrier (foil or roofing felt)
- Lean concrete leveling layer
- Anti-shrinkage reinforcement ϕ6 mm every 15 cm
Polystyrene block pools:
- Stable subgrade compacted to Is=0.95
- Sand-cement mixture bedding
- Thermal insulation (XPS polystyrene 5-8 cm)
- Protective foil against puncture
Insulation and Protection Systems
Moisture barrier:
- PVC foil 1.5-2.0 mm or TPO
- Overlap welding with tightness control
- Insulation extension 30 cm above ground level
- Mechanical protection (geotextile, protective plates)
Thermal insulation:
- XPS polystyrene under bottom slab (8-12 cm)
- Wall perimeter insulation (5-8 cm)
- Thermal bridge prevention
- Edge and corner insulation
Under-slab drainage:
- 8-16 mm gravel layer, thickness 20-30 cm
- PVC drain pipe ϕ100 mm
- Control manhole with pumping possibility
- Connection to main property drainage system
Subgrade Quality Control
Compaction tests:
- In-situ bulk density measurement
- Required compaction degree Is ≥ 0.95
- Tests every 25 m² surface
- Results documentation in construction log
Geodetic measurements:
- Elevation control every 2x2 m
- Deviation tolerance: ±2 cm
- Slope checking (2-3% toward drain)
- Final measurement before concreting
Permeability tests:
- Infiltration test (for cohesive soils)
- Assessment of additional drainage need
- Stability test when saturated
- Photographic documentation
10. Environmental and Legal Aspects
Environmental Protection During Earthworks
Minimizing impact on nature:
- Preserving existing vegetation outside work zone
- Protecting soil from fuel contamination
- Proper storage of construction materials
- Reclamation of temporarily occupied areas
Stormwater management:
- Drainage system from construction site
- Preventing soil erosion
- Protection against groundwater contamination
- Compliance with local development plan
Noise and dust limitation:
- Work hours 7:00-20:00 (working days)
- Site spraying during dry weather
- Covering transported excavated material
- Vehicle wheel cleaning before leaving property
Legal Requirements Specific to Mazovia
Archaeological monument protection: According to the monument protection act, in case of discovering objects that may have archaeological significance during earthworks, the following is required:
- Immediate work stoppage
- Notification of Mazovian Voivodeship Monument Conservator
- Securing the discovery site
- Possible work delay of 2-4 weeks
Groundwater protection:
- Prohibition of introducing contaminants to soil
- Obligation to monitor water quality during dewatering
- Need to obtain water law permit for larger water intakes
- Documentation of pumped water quantities
Municipal regulations regarding pools:
- Warsaw: notification requirement for pools >25 m² surface
- Piaseczno, Konstancin-Jeziorna: additional architectural requirements
- Legionowo, Marki: restrictions in water intake protection zones
- Ożarów Mazowiecki: stormwater management requirements
Insurance and Liability
Contractor civil liability insurance:
- Minimum guarantee sum: 500,000 PLN
- Extension for third-party property damage
- Environmental damage protection
- Protection period: work duration + 12 months
Quality guarantees for completed work:
- Earthworks guarantee: 12 months
- Drainage system guarantee: 24 months
- Possible extension with premium materials
- Post-completion documentation as guarantee condition
11. Work Schedule and Seasonal Factors
Optimal Timing for Earthworks
Season I - Spring (March-May): Advantages:
- Stable groundwater level after snowmelt
- Moderate soil moisture
- Possibility of completion before swimming season
Disadvantages:
- High service prices (peak season)
- Limited availability of contractors
- Possible delays due to unstable weather
Season II - Summer (June-August): Advantages:
- Best weather conditions
- Lowest groundwater level
- Optimal conditions for soil compaction
Disadvantages:
- Highest service prices of the year
- Need for intensive spraying during droughts
- Very limited contractor availability
Season III - Autumn (September-November): Advantages:
- Lower service prices (30-40% cheaper than summer)
- Better contractor availability
- Stable weather conditions in September
Disadvantages:
- Rising groundwater level
- Risk of precipitation and excavation undermining
- Impossibility of pool use until next year
Season IV - Winter (December-February): Advantages:
- Lowest prices (up to 50% cheaper)
- Full contractor availability
Disadvantages:
- Soil freezing (additional thawing costs)
- Transport difficulties during snowfall
- Limited soil compaction possibilities
Typical Work Schedule (8x4 m pool)
Week 1-2: Preparations
- Obtaining permits and consents
- Material delivery and storage
- Site layout and marking
- Vegetation protection
Week 3: Preliminary Excavations
- Topsoil removal
- Excavation to 1.0 m depth
- Utility location and protection
- Temporary dewatering installation
Week 4: Target Excavations
- Deepening to target dimensions
- Wall and bottom shaping
- Auxiliary excavations (manhole, installations)
- Geodetic controls
Week 5: Protection and Subgrade
- Excavation wall stabilization
- Subgrade preparation (compaction, bedding)
- Perimeter drainage installation
- Geotextile and insulation laying
Week 6: Finishing
- Quality controls and approvals
- Site cleanup
- Post-completion documentation
- Preparation for next stage (pool structure)
12. Earthworks Cost Estimate
Detailed Cost Calculation (2025)
Standard 8x4x1.5 m pool in sandy soils:
Labor and equipment:
- Machine excavation (65 m³): 35 PLN/m³ × 65 = 2,275 PLN
- Hand excavation near utilities (8 m³): 80 PLN/m³ × 8 = 640 PLN
- Shaping and finishing: 1,200 PLN
- Total labor: 4,115 PLN
Materials:
- Sand for subgrade (12 m³): 45 PLN/m³ × 12 = 540 PLN
- Gravel for drainage (8 m³): 60 PLN/m³ × 8 = 480 PLN
- Geotextile (50 m²): 12 PLN/m² × 50 = 600 PLN
- Drain pipe (25 m): 25 PLN/m × 25 = 625 PLN
- Total materials: 2,245 PLN
Temporary dewatering:
- Wellpoints with pump (20 m): 180 PLN/m × 20 = 3,600 PLN
- 4-week operation: 200 PLN/week × 4 = 800 PLN
- Total dewatering: 4,400 PLN
Transport and disposal:
- Excess soil removal (25 m³): 35 PLN/m³ × 25 = 875 PLN
- Material delivery: 800 PLN
- Total transport: 1,675 PLN
TOTAL COST: 12,435 PLN
Factors Affecting Price
Additions to base price:
Difficult soil conditions (+20-40%):
- Clay soils requiring drying
- High groundwater (need for deep wells)
- Rocky soils or those with large stones
Difficult accessibility (+15-30%):
- No excavator access (hand work)
- Narrow entrance gate (<3 m)
- Need for manual transport
Additional requirements (+10-25%):
- Valuable vegetation protection
- Work in monument protection zone
- Special drainage requirements
Price seasonality:
- Spring (March-May): base price +20%
- Summer (June-August): base price +40%
- Autumn (September-November): base price -10%
- Winter (December-February): base price -30%
Cost Comparison for Different Pool Sizes
6x3x1.2 m pool (small):
- Excavation volume: 28 m³
- Earthworks cost: 8,500-11,200 PLN
- Unit cost: 300-400 PLN/m³
10x5x1.5 m pool (medium):
- Excavation volume: 95 m³
- Earthworks cost: 16,800-22,400 PLN
- Unit cost: 175-235 PLN/m³
15x7x2.0 m pool (large):
- Excavation volume: 280 m³
- Earthworks cost: 42,000-58,800 PLN
- Unit cost: 150-210 PLN/m³
Conclusions: Unit costs decrease with increasing pool size due to economies of scale.
13. Common Problems and How to Avoid Them
Groundwater-Related Problems
Problem: Water inflow to excavations
Causes:
- Incorrect groundwater level assessment
- Not considering seasonal fluctuations
- Lack of or insufficient dewatering
Solutions:
- Deepening wellpoint system
- Additional dewatering wells
- Temporary chemical soil stabilization
Prevention:
- Thorough hydrological investigations
- Measurements in different seasons
- Consultations with local contractors
Problem: Pool structure displacement
Causes:
- Lack of perimeter drainage
- Improper water discharge
- Seasonal groundwater level rise
Solutions:
- Permanent dewatering system installation
- Structure loading (additional mass)
- Ground anchors in extreme cases
Prevention:
- Mandatory drainage for all pools
- Well with automatic pump
- Alarm system monitoring water levels
Excavation Stability Problems
Problem: Excavation wall sliding
Causes in Mazovian soils:
- Clay soils lose cohesion when saturated
- Loose sands in saturated state
- Exceeding natural slope angle
Immediate solutions:
- Reducing slope angle to safe level
- Installing bracing casing
- Unstable zone dewatering
Prevention:
- Proper geotechnical parameter assessment
- Casing excavations deeper than 1.5 m
- Wall displacement monitoring
Problem: Adjacent building foundation undermining
Causes:
- Lowering groundwater level
- Changing water flow directions
- Soil erosion under foundations
Solutions:
- Immediate dewatering cessation
- Sealing injection under foundations
- Building technical condition monitoring
Prevention:
- Analysis of impact on adjacent buildings
- Limiting dewatering range
- Third-party property damage insurance
Soil Quality Problems
Problem: Organic soil discovery
Characteristics:
- Peat, silt, soils with high humus content
- Low bearing capacity, high compressibility
- Impossibility of direct pool placement
Solutions:
- Soil replacement to 0.5-1.0 m depth
- Reinforcing geogrid application
- Cement or lime stabilization
Additional costs:
- Soil replacement: 150-250 PLN/m³
- Geogrid: 15-25 PLN/m²
- Stabilization: 200-400 PLN/m³
14. Quality Control and Approvals
Earthworks Documentation
Construction log:
- Weather conditions each work day
- Work progress with description of completed work
- Quality controls and measurements
- Supervisor inspector comments
Photographic documentation:
- Site photos before work commencement
- Excavation stages every 0.5 m depth
- Soil condition at each level
- Dewatering and protection systems
Geodetic measurements:
- Pre-commencement inventory
- Control measurements every 2 days
- Final measurement before next stage
- Documentation in as-built drawing form
Approval Procedures
Earthworks approval - control list:
Excavation geometry:
- ☐ Dimension compliance with design (tolerance ±5 cm)
- ☐ Right angle checking by diagonal method
- ☐ Bottom slope control (minimum 2% toward drain)
- ☐ Bottom flatness check (tolerance ±2 cm/2m)
Subgrade quality:
- ☐ Soil compaction (Is ≥ 0.95)
- ☐ Subgrade bearing capacity (plate load test)
- ☐ No standing water in excavations
- ☐ Loose soil fragment removal
Dewatering systems:
- ☐ Perimeter drainage according to design
- ☐ Drain pipe slopes (min. 0.3%)
- ☐ Control and inspection manholes
- ☐ Water flow test through system
Safety:
- ☐ Excavation wall stability
- ☐ Excavation marking and protection
- ☐ Evacuation route accessibility
- ☐ Environmental measurement protocols
Documents Required at Approval
- Earthworks approval protocol
- Control geotechnical test results
- As-built drawings with geodetic measurements
- Soil compaction test protocols
- Drainage system documentation
- Applied material quality certificates
- Site transfer protocol for next stage
Summary
Building a garden pool in the Mazovian Voivodeship requires detailed planning and a professional approach to earthworks. Key to investment success are:
Thorough soil-water condition recognition - geotechnical investigations are an investment that pays back multiple times by avoiding problems during implementation
Proper technology selection - adapting excavation methods to local geological conditions
Comprehensive dewatering approach - both temporary (during construction) and permanent (operational)
Compliance with legal requirements - particularly important in the context of environmental protection and archaeological monuments
Choosing an experienced contractor - knowledge of local conditions and pool work specifics
Average earthworks cost for a standard family pool is 12-18 thousand PLN, but can increase even twofold in difficult soil conditions. Optimal implementation timing is early autumn (September-October) due to favorable price-to-working conditions ratio.
Remember that properly executed earthworks are the foundation for long and trouble-free pool operation. Savings at this stage can result in costly repairs in the future, so it's worth investing in professional execution from the very beginning.
Bibliography and Sources
- PN-83/B-03010 - Retaining walls. Static calculations and design
- PN-88/B-04481 - Construction soils. Soil sample testing
- Regulation of the Minister of Infrastructure of April 12, 2002, on technical conditions that buildings and their location should meet
- Act of July 20, 2017, Water Law
- Guidelines for designing an
Tags
Share this guide
About the author
mgr inż. Piotr Kowalczyk
Earthworks Specialist | Tree Group
Category
Earthworks
Reading time
16 minutes
Publication date
May 22, 2025
Similar guides
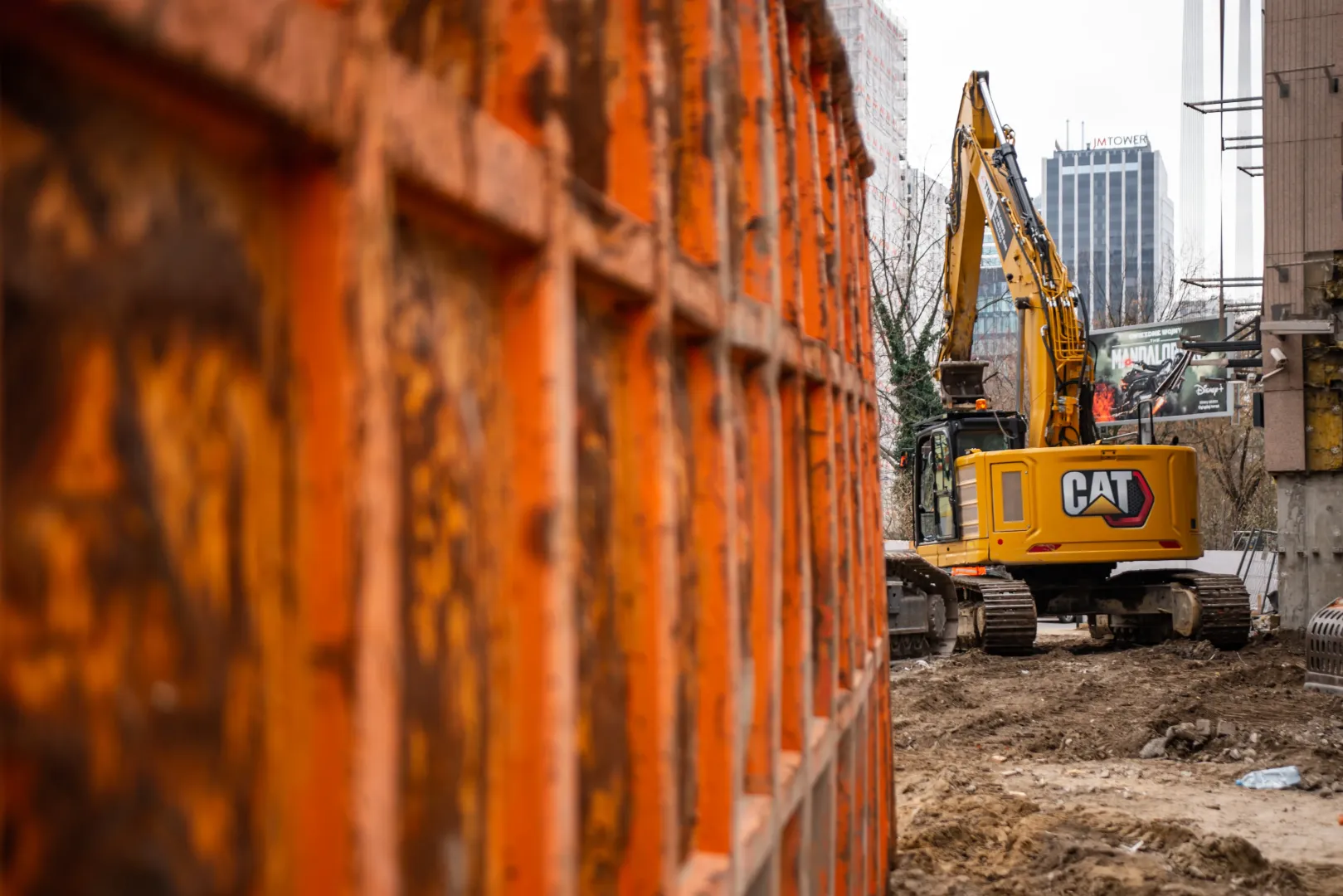
Starting and Shutting Down Liebherr Machines - Operator's Guide
Comprehensive instruction guide for Liebherr machine operators, presenting correct procedures for starting and shutting ...
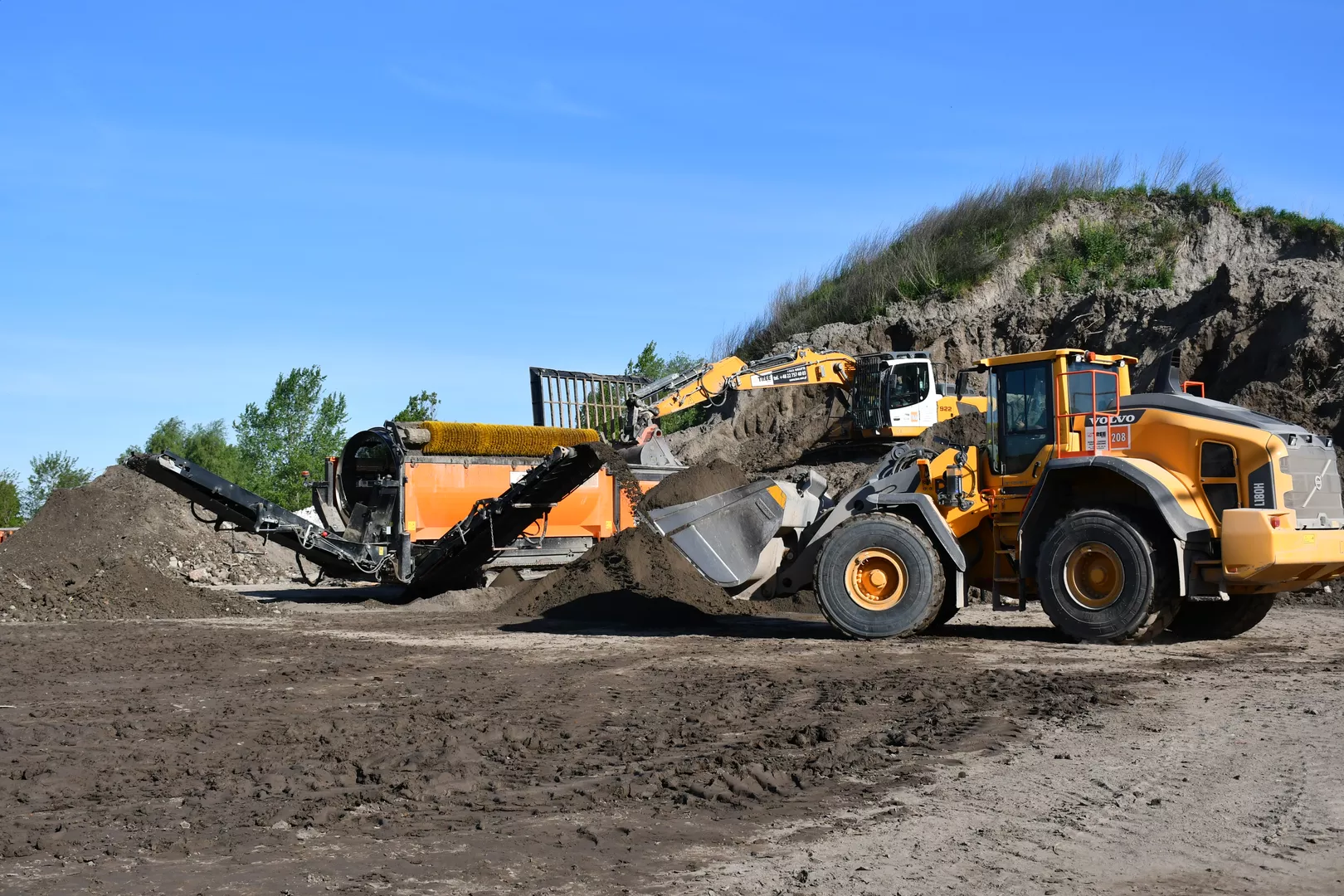
How to Prepare Land for Single-Family House Construction Around Warsaw - Comprehensive Guide
A practical guide covering all stages of land preparation for house construction in Mazovian Voivodeship, taking into ac...